
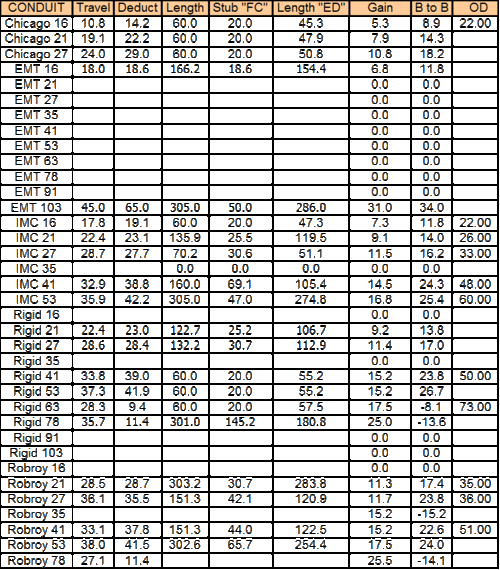
This leads to the preference for relatively lightweight materials, but controlling springback after forming presents a challenge for processing-sensitive lightweight alloys. The constant striving for cost reduction, quality improvement, and lightweighting of products is a significant challenge to many manufacturing industries. Since the difference in springback measurement between the proposed and the conventional methods was within 0.15° on average, it is demonstrated that the laser tracking, on-machine measurement is a feasible real-time springback measurement technique for Industry 4.0.

In this paper, bending experiments were conducted with AA6082 rectangular hollow profiles bent at 30°, 45°, 60°, and 90° angles, and springback angles from the conventional manual measurement were compared to that from the on-machine measurement. An image processing technology is integrated with the manufacturing process to track the deformation and measure springback angle in real time, eliminating the need for the workpiece to be transferred to a measurement device. An on-machine measurement technique is therefore developed to measure springback in rotary draw bending with an affordable laser and a webcam. However, this trial-and-error is costly for batch production in manufacturing. The realized bend angle has to be measured for springback compensation before removing the profile from the machine, and the bending process can follow an iterative approach until the product quality is satisfied. Due to the elastic recovery of the material, springback compensation to control the bent product quality is one of the critical manufacturing issues. Rotary draw bending is a commonly used metal forming technique for profile bending.
